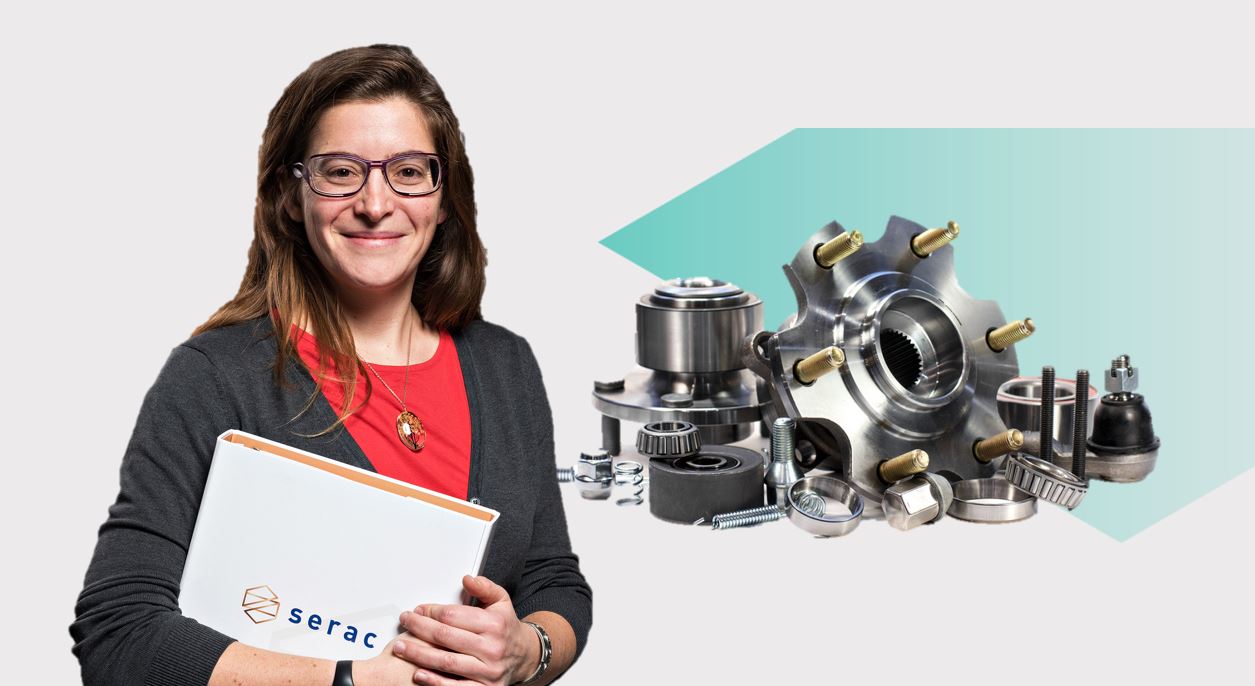
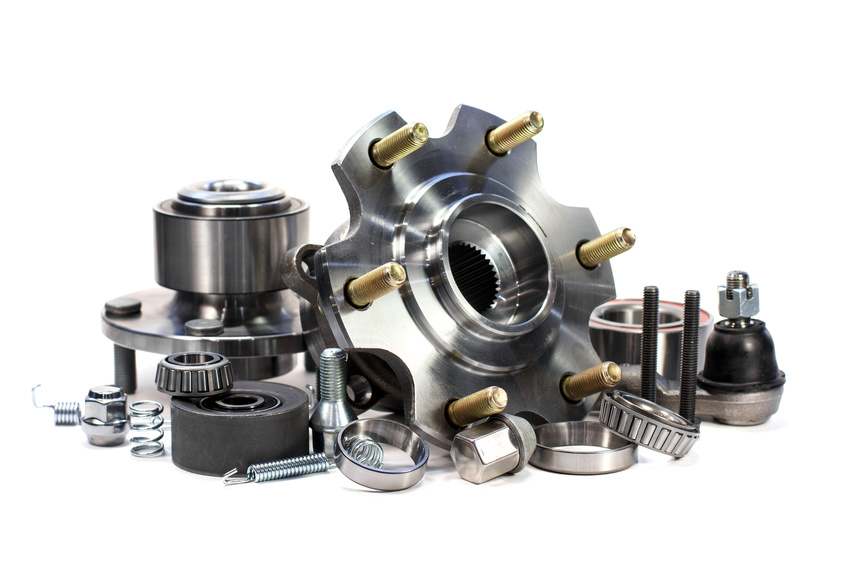
Excess stock, unused spare parts and additional costs are extremely commonplace in the absence of a functioning synergy between supplier and customer. It is our aim to identify the 5 key points which enable both a reduction in stock levels and improvement of the service rate of spare parts.
1. Clearly define your stock of critical parts
An estimated 80% of spare parts are rarely used during the operating life cycle of the machine (no movement for several years). However, the day these parts do finally fail, a production stoppage is almost inevitable. To avoid the extra costs generated by urgent delivery, or the need to maintain an excessively large stock, ask the manufacturer to clearly identify all critical parts.
If you consume a large number of parts, you could possibly opt for creation of a consignment stock. You only pay a percentage of this stock each year and your consumption is invoiced after the annual stock taking.
Give preference to a manufacturer with a global distribution network and subsidiaries in order to reduce transport costs and shipping times.
2. Make full use of the manufacturer's terms of warranty
Purchasing a batch of critical spare parts at the same time as the machine is often a good way of obtaining substantial discounts.
In this way, you are also sure to have parts from the same production batch as those used on your new machine and thus avoid the inconveniences related with different versions or even obsolescence.
Of course, during the warranty period, any parts found to be of faulty manufacture or not fit for purpose will be replaced free of charge.
Certain manufacturers include labour costs in their part warranty and take entire charge of logistics, repair and return to production of your equipment.
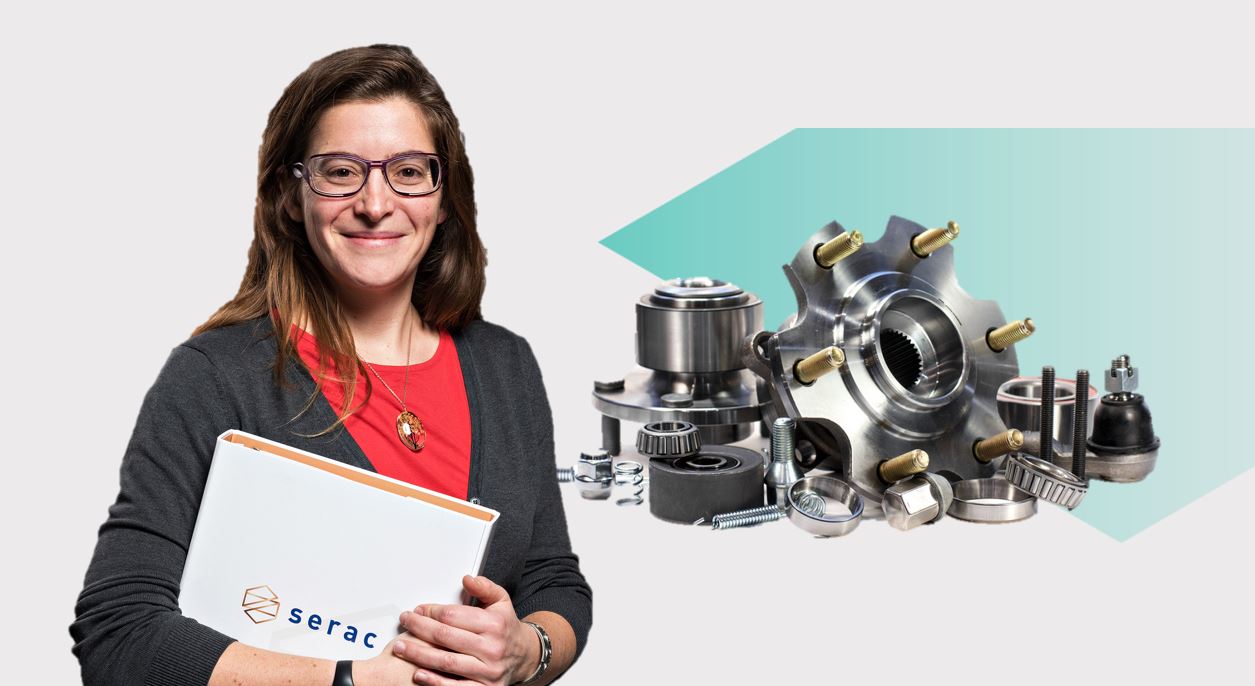
3. Request a customised maintenance scheme
Above and beyond the theoretic maintenance schedule proposed during installation, you may want to ask your equipment supplier to take into account the true operating conditions of your machine, for example after 6 months of operation.
A customised planned maintenance schedule will enable you to anticipate orders and negotiate additional discounts. You may also choose a maintenance contract with monthly payments. Don’t hesitate to ask for information.
4. Avoid having to send back non-compliant parts
To manage obsolescence or incompatibility of parts, ask your manufacturer to keep you informed in a proactive manner and to propose proven alternatives.
By working with a single contact partner who manages all spare parts, including those of partner suppliers, you will simplify the process and reduce ordering errors.
5. Take advantage of the free services proposed by the manufacturer
To manage obsolescence or incompatibility of parts, ask your manufacturer to keep you informed in a proactive manner and to propose proven alternatives.
By working with a single contact partner who manages all spare parts, including those of partner suppliers, you will simplify the process and reduce ordering errors.