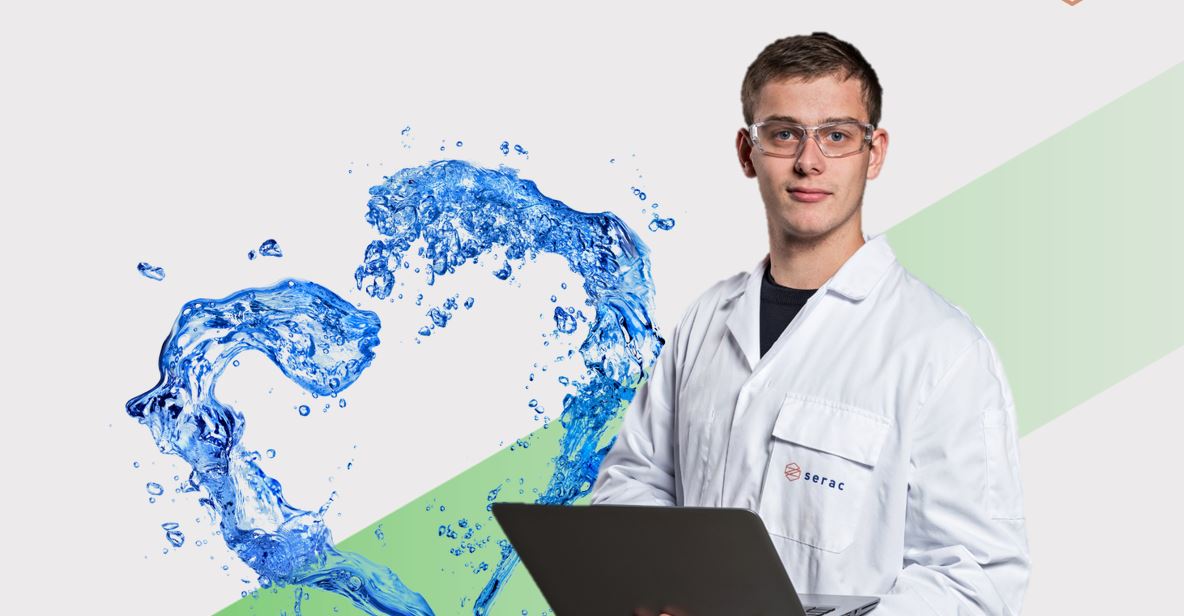
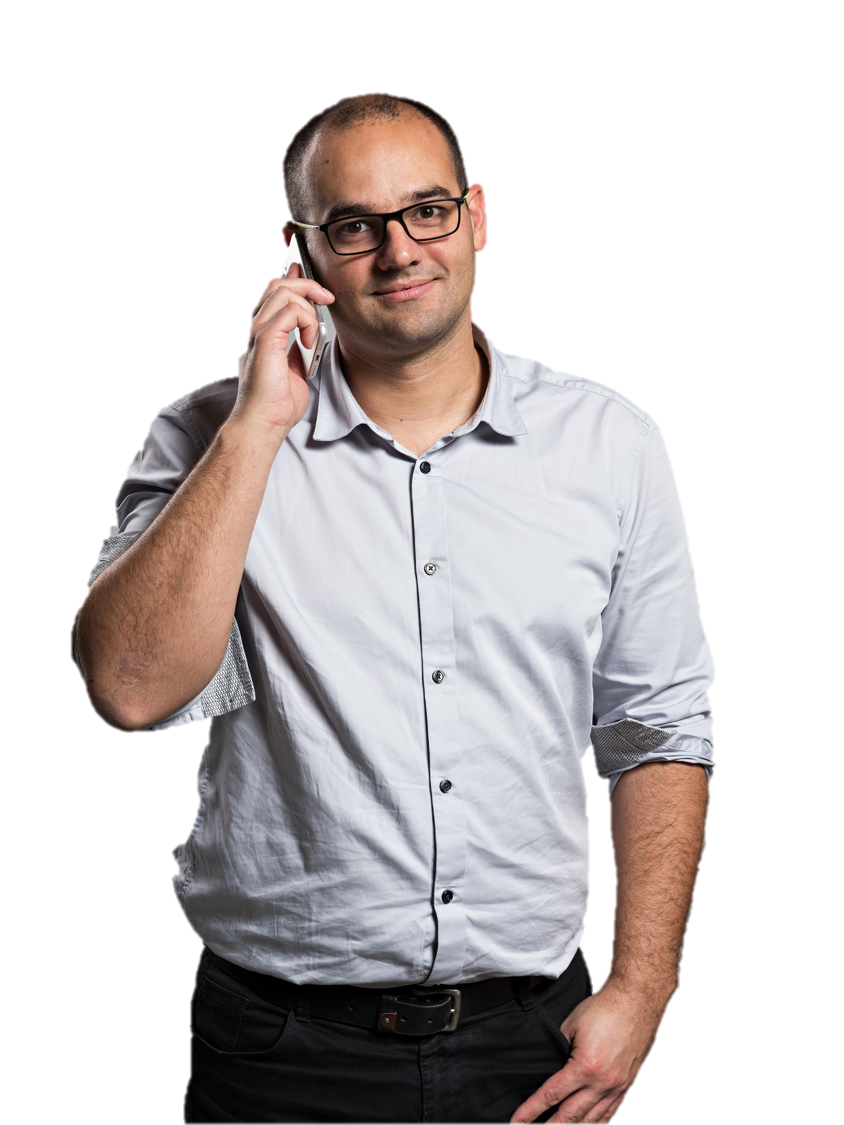
Arnaud Rosier
Serac is committed to working in close partnership with its customers in order to enhance the performance of their equipment all through the operational life. From this long-term cooperation arise simple or sometimes more complex solutions which increase the productivity and reduce the environmental impact of packaging lines.
Arnaud Rosier’s team, customer service manager at Serac France, helped a worldwide leader in the cosmetics industry to optimize tank cleaning on a conditioner line. As a result, the cleaning time has been halved and water consumption divided by 7.
3 Steps to optimize the cleaning cycles on a packaging line
Step 1: Pinpoint deviations using process data
During an on-site performance audit, our technicians, who know the ins and outs of cosmetic products and production environment, noticed that cleaning cycles were abnormally long and effluent water volume far bigger than it ought to be. In order to precisely spot the origin of these deviations, they installed on the control unit a new function which records all cleaning cycles.
“ A new function which records all cleaning cycles installed on the control unit, enabled us to analyze each step of the cleaning process by comparing real and theoretical durations. The analysis revealed the key parameters to act on, in this case water temperature and mechanical action. “
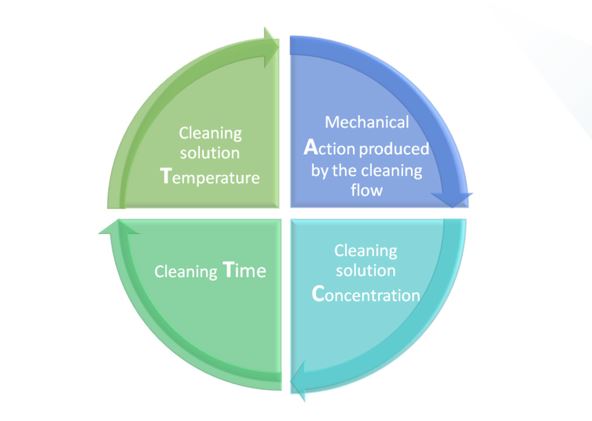
T.A.C.T. parameters
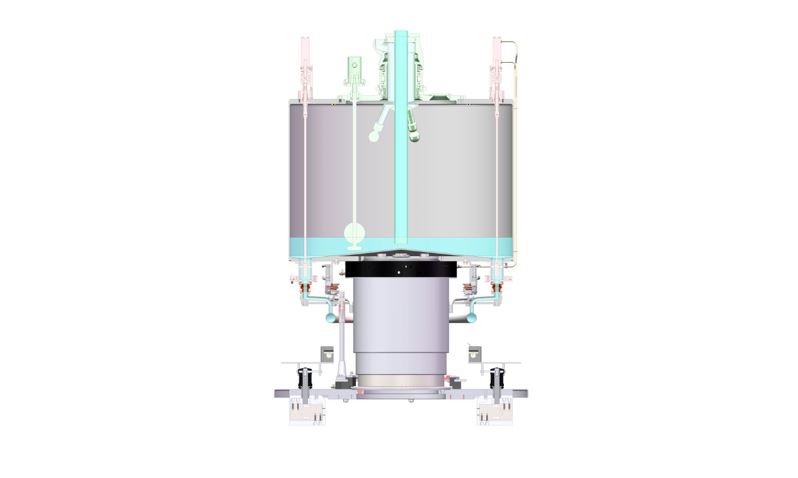
Step 2: Implement targeted improvements on the cleaning system
Our technicians then suggested fairly simple improvements targeted on the identified parameters.
They installed on the CIP system an automatic collector with water circulation in order to better manage the heating and cooling steps, and placed in the tanks high performance multi-directional spray balls to increase the mechanical power of water. They also placed viewfinders on the pipelines to offer a better control of fluids during the cleaning cycle. At the end of this phase, the CIP system was mechanically
ready to reach the expected results.
Step 3: Review the cleaning cycle program
Our team still had to check the valve beat cycles (time and level control) and validate the performance for each step of the cleaning cycle before reviewing the automation programs. The graph below depicts the cleaning cycle before and after the optimization work: we gained 35 minutes, essentially on the washing stage which now only requires one cycle and 5 minutes against 2 cycles and 34 minutes previously !
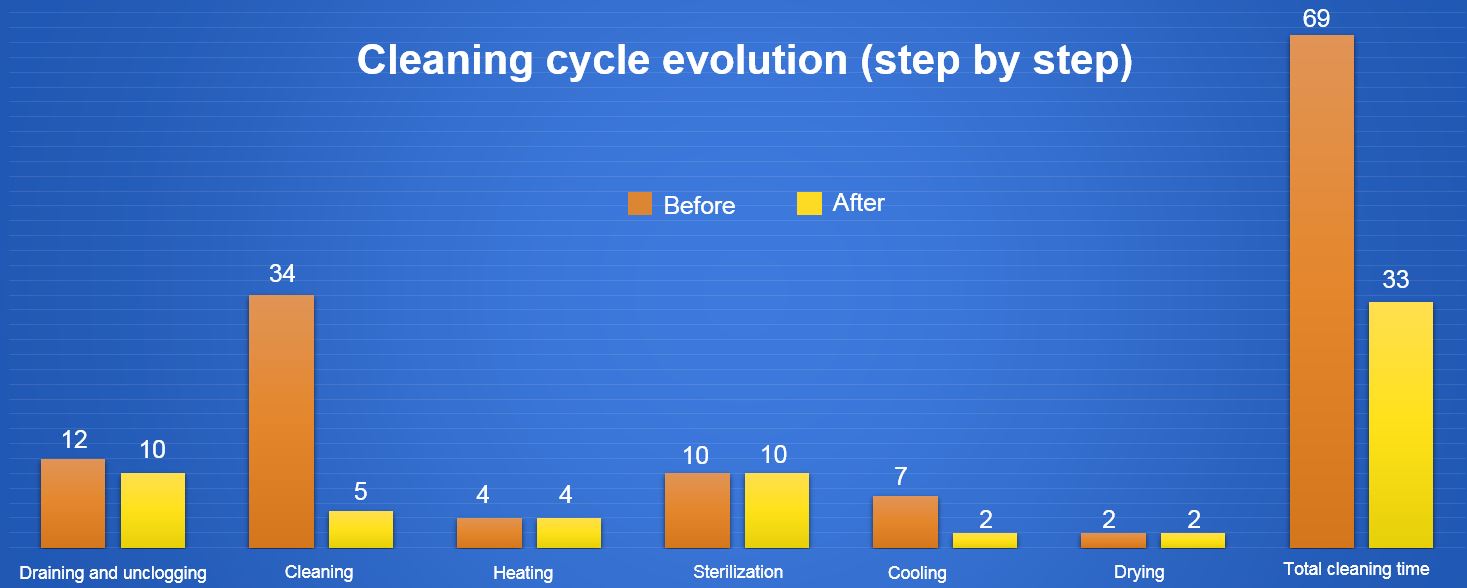
Cleaning cycle optimization is only one of the numerous services we can offer worldwide through our dedicated teams.
Do not hesitate to contact us for more information.