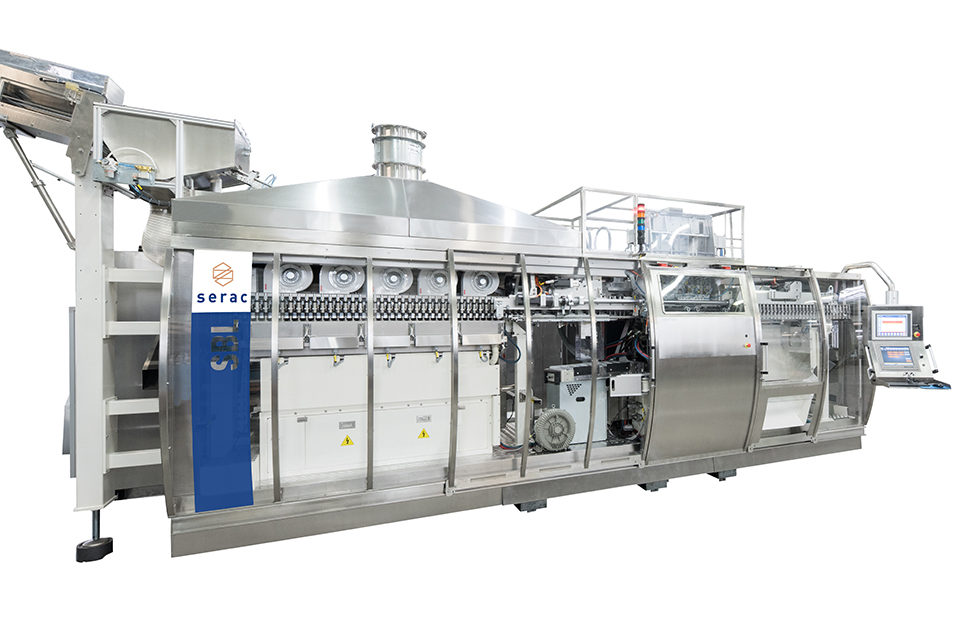
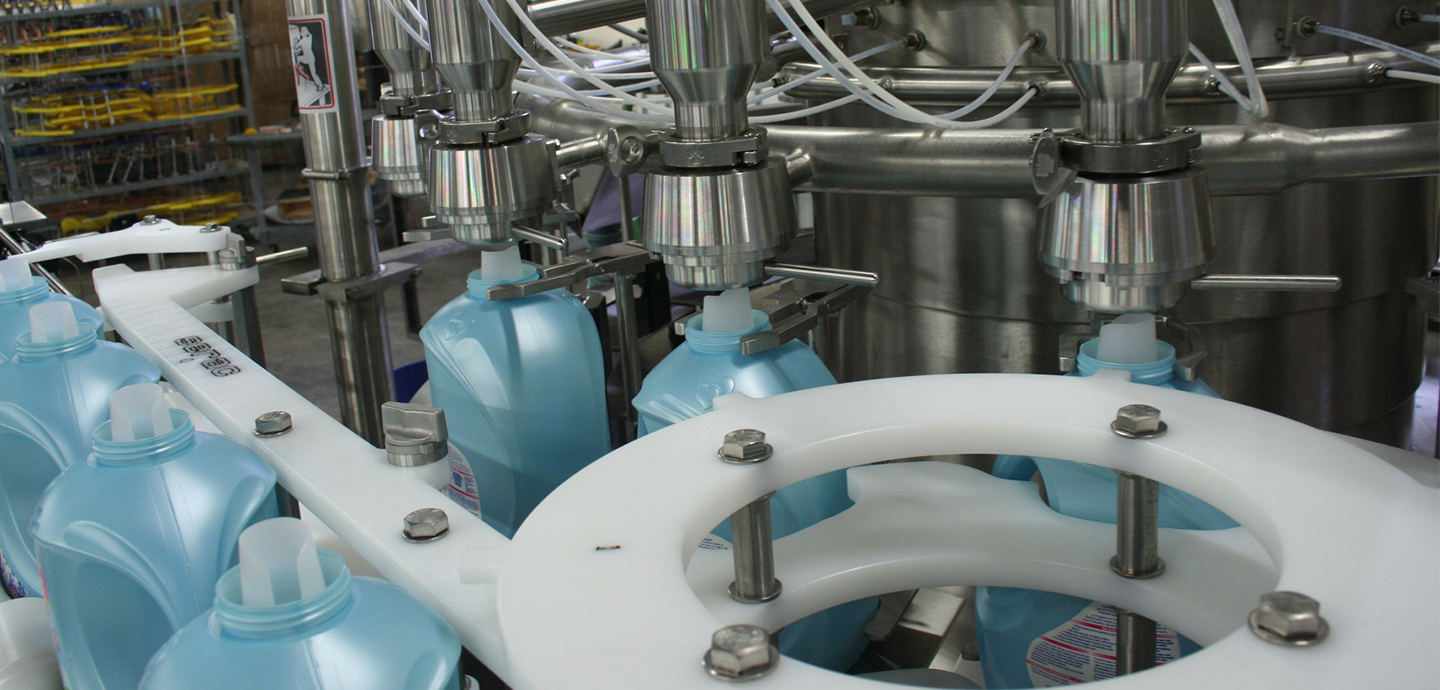
1- Clear PET bottles of any shape blown in-house
In-house bottle manufacturing offers obvious benefits on procurement and storage costs (plastic preforms are much smaller than bottles) as well as on quality (no risk of having bottles scratched or distorted during transportation and handling), PET is becoming more and more popular for HPC products since it allows to produce transparent and squeezable bottles of any shape with extremely precise neck finish. All this with benefits on raw material cost, energy consumption and recycling.
Serac has developed state-of-the-art PET stretch blow molding units that combine quality with flexibility: they provide ultimate control of the blowing process on round, oval or flat bottles as well as the possibility to switch quickly from one to another. The preferential heating option is installed and removed without tools in just 15 minutes and mold changeovers require only 10 minutes.
Particularly reliable and efficient, Serac’s stretch blow molders can produce up to 18,000 bottles of 500 ml per hour, with an efficiency rate over 98%.
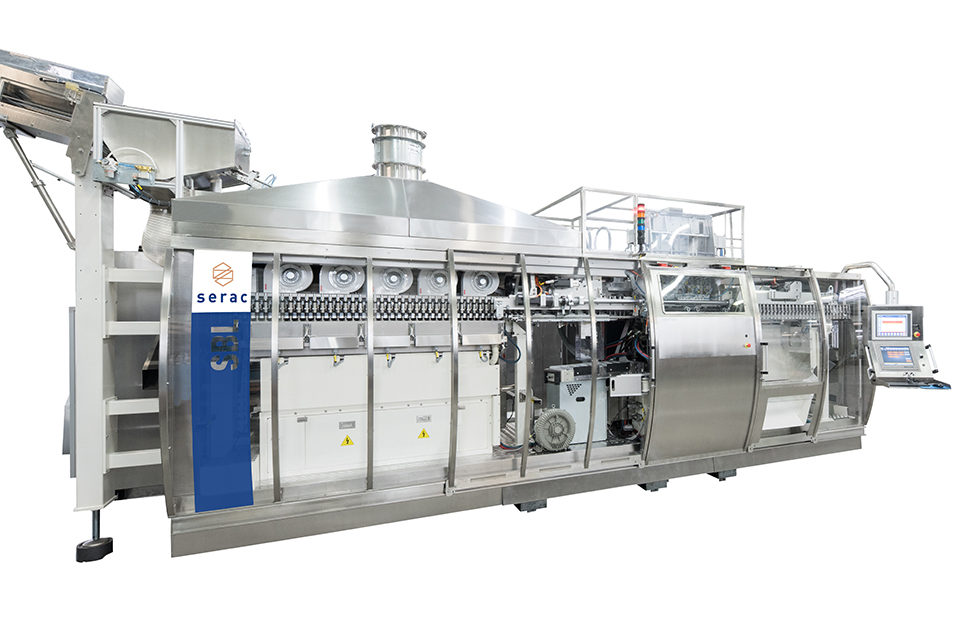

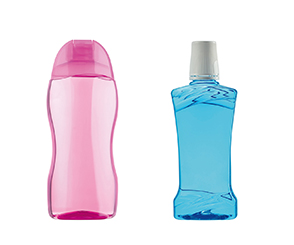
up to 18,000 containers per hour (500ml)
Efficiency rate over 98%.
2- Filling units approved for process optimization
The weight filling technology can be a real asset for process optimization on highly segmented markets.
First, it is adapted to all kinds of products (liquid, viscous, sticky, foaming) and can accommodate a size ratio of 1 to 20 where volumetric filling can only cope with a ratio of 1 to 6; the same equipment can thus be used for a wide production range with a minimum number of tooling changeovers.
However, more importantly, weight filling is the only technology that can apply for an « Automatic Weighing Instrument » (AWI) type approval and thus be used for legal measurement.
The AWI type approval obtained by Serac for its latest generation of weight fillers allows manufacturers to make sure they conform to the nominal quantity printed on their packaging while drastically lightening their product sampling and eliminating the need of slightly overfilling containers to offset deviations of the filling system: efficiency is increased through time and product savings.
3- New dosing and cleaning systems to increase production capacity
For the HPC market, Serac has developed small pressurized tanks combined with specific dosing systems that can reduce the dosing time up to 20%. These tanks are 100% self-draining, with no dead corners where product could be retained. They can also be fitted with an additional vacuum pump to reduce flushing time.
The CIP solutions proposed by Serac work in closed circuit and use multidirectional spray balls so that filling units can be cleaned quickly, with a minimum of effluents. The cleaning procedure can be automated and run in sequence to further reduce production downtimes.
Serac is also offering new dosing solutions to support product innovation on the HPC market, such as bi-phase cleansers, the addition of scents to traditional liquid bleach, filling dual chamber packaging, or alternate filling of several fragrances for retail ready packaging.
4- One single turret for both pushed on and screwed cap
To offer maximum versatility to industrial manufacturers, Serac has developed eTCS, a brushless servo drive capping turret. This turret has been designed for sensitive and complex applications that require caps to be precisely oriented and torque effort to be constantly monitored and registered.
eTCS can manage all kinds of caps encountered on the HPC market, even the most innovative ones and change-overs are reduced to a strict minimum.
5- Single block blow-fill-cap units for maximum efficiency in minimum space
Convinced that fully synchronized lines, where all components work together as a single unit, can provide a competitive advantage to many industrial manufacturers, Serac has developed single block units that associate a stretch blow molder, a rotary weight filler and a capping turret.
Perfect synchronization is achieved through a unique patented transfer system that converts the sequential motion of the stretch blow molder into continuous motion, adapted to the rotary filler and ensures constant adjustment of the filler-capper to the blow molder’s output. Servo drives used all along the line offer a high level of precision and repeatability.
Positive transfer of preforms and bottles all along the process eliminates the need for conveyors and accumulation areas, thus saving up to 25% on the lines’ footprint, ensures bottle stability and positioning and avoids jams and scratches.
Single block units require a single person to operate and are also much easier to maintain. They also offer significant energy savings and greatly simplified changeovers.