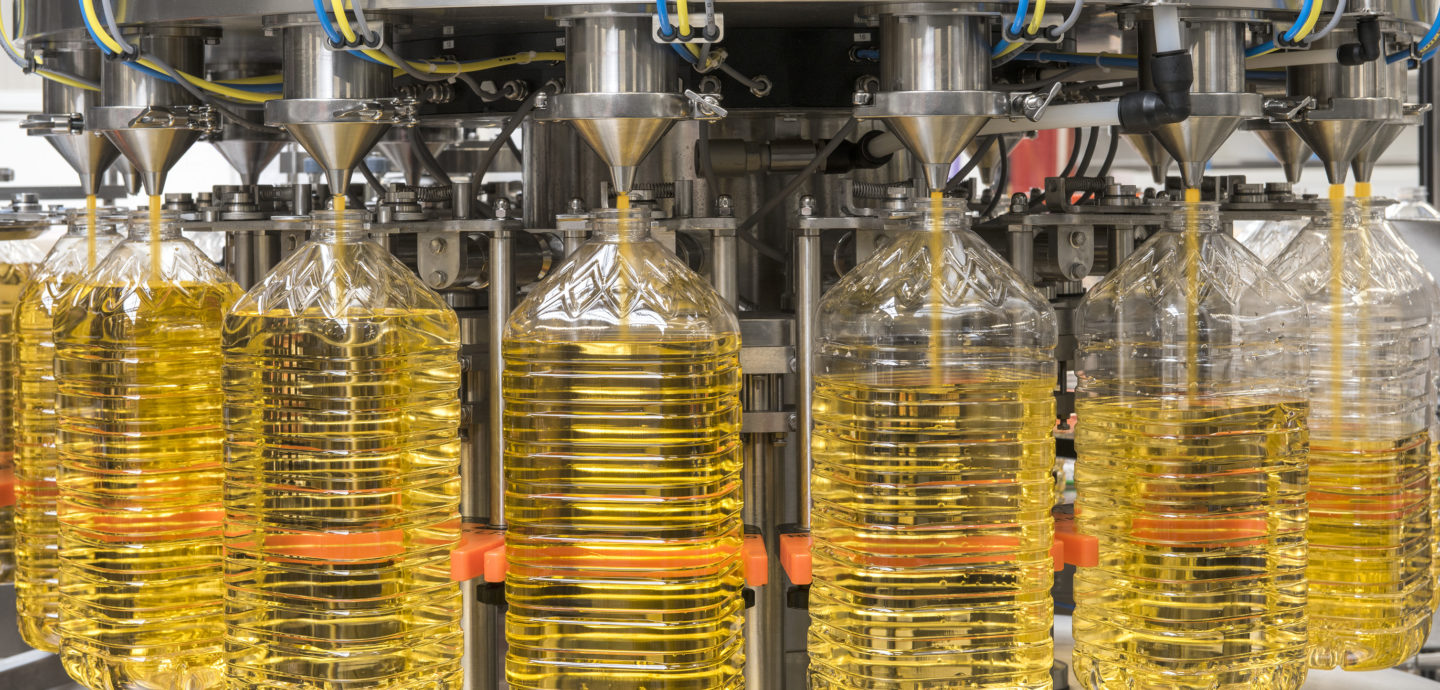
Olive oil filling
Manufacturers who wish to move to PET bottles can choose between two main options: stand-alone machines linked with conveyors or integrated blow-fill-cap blocks. Serac, a key player in oil filling for more than 30 years supplying leaders of the oil industry, with 300 machines installed worldwide amongst which several in Spain at Borges and Ybarra, offers both. However, the market appears to favor integrated blocks which enable to use thinner bottles, save space and can be run by a single operator. These blocks also meet oil manufacturers’ requirements in terms of dosing output, cleanliness and accuracy with Serac’s weight filling technology.
Avoid open-air conveying of uncapped bottles
On integrated blocks, bottles are positively transferred by the neck from blowing to capping, over a minimum distance and within a closed area. The removal of conventional conveyors, where bottles are pushed together through an open-air journey, avoids external pollution and accidental spillage especially when bottles are accelerated or stopped.
Manage filling speed
Serac’s integrated blocks benefit from all the OEM’s expertise in edible oil filling. The weight fillers specifically designed for edible oil can for example be fitted with conical vacuum valves which open gradually. These valves noticeably reduce swells at the bottom of the bottle and oil aeration. The line speed can be increased with no risk of dripping and bottles remain perfectly clean.
Serac can also manage complex filling cycles varying the flow rate from the beginning to the end: a real benefit for big bottles which can thus be filled faster though still very cleanly.
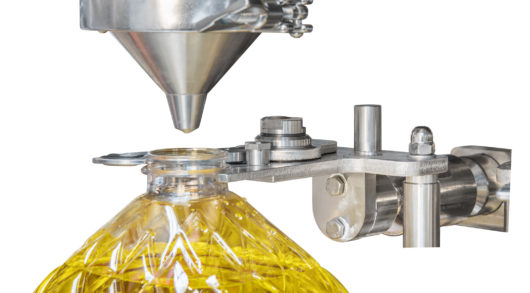
Control the final drop
To avoid overdosing, the quantity of oil still flowing after the valve is closed must be perfectly controlled. On its fillers, Serac is constantly measuring and adjusting it. And the bottle is never soiled thanks to the vacuum valves which suck back the last droplet in a buffer tank mounted above the main one.
Use a dosing system which is not sensitive to temperature and aeration
For a product as olive oil, whose volume varies with changes in temperature and which is highly subject to aeration, weight filling remains the most accurate and reliable technology: 1kg remains 1kg, whatever the temperature.
Serac has developed extremely accurate weight fillers (with standard deviation between 0,3 and 0,5 g for 1 liter) which can be homologated for legal metrology. With such fillers, the quantity is correct as of the first bottle produced and quality controls can be lightened. Product losses due to setting operations and overdosing are reduced, and so are downtimes as well as changeover times.
The medium and high output blow-fill-cap blocks from Serac give olive oil manufacturers the possibility to reduce their manufacturing costs with onsite blowing while keeping a high-performance level on filling. They allow to produce bottles ranging from 250 ml up to 5 liters with various designs, including attached handles for the biggest ones, and have been designed to offer maximum flexibility with shorter changeover times at each step. They can also include the eMC capper module for spray insertion in premium oil bottles.
Serac’s weight filling and capping machines remain a reference as well on the edible oil market, whatever the packaging material (aluminum, glass, PET) and the output required.
上一篇:The Modulo nozzle is now available for all Form-Fill-Seal (FFS) cup packaging lines
下一篇:Jean-Jacques Graffin maintains innovation at Serac for 50 years
相关文章
-
食用油灌装机
自1969年,斯拉克集团Serac就是食 ...