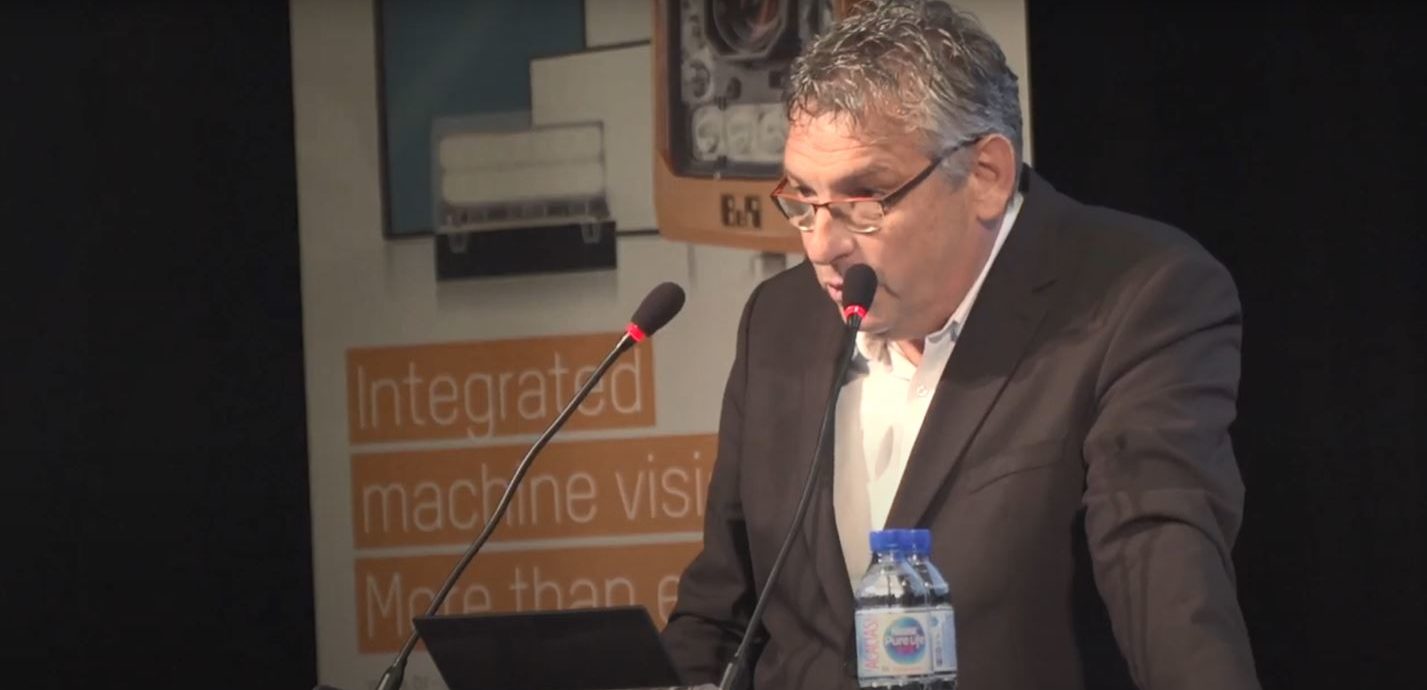
An interview of Thierry Deau – CTO
Chief Technical Officer and member of the Executive Commitee of Serac Group, Thierry Deau has a deep expertise of the packaging industry and has been following closely, over the past few years, how it addresses digital transformation.
He explains us what such a transformation means for industrial manufacturers as well as for OEMs like Serac.
Thierry Deau – Chief Technical Officer
Is Industry 4.0 compulsory for packaging activities ?
TD: “For consumer goods yes, it’s obvious. Simply because the new manufacturing technologies and the concept of connected factory enable to meet the expectations of the digital consumer we have all become : customized products, immediately available and ‹ transparent › products which we can be confident with and easily compare.”
Within what timeframe?
TD: “I believe that in 10 years, connected production lines will be considered as a standard. Until then, we still have a lot to work on and many barriers to lift. The main one is human, because data collection and connectivity are worrisome issues. As long as industrial manufacturers won’t clearly see what benefits they can get from Industry 4.0 and won’t be reassured about security, they will hesitate to go for it. But things are changing fast. Interoperability for example is no longer an issue with the development of non-proprietary standards such as OPC-UA.”
For what particular needs?
TD: “Smart machines are above all made to provide ultimate performance, with as little dowtime as possible, and real-time support to operators. The main objective is to implement predictive maintenance : being able to spot any deviation in the process and to anticipate breakdowns in order to ensure top quality production over the longest possible period. The second is to give operators the right information at the right time to help them make the best decision when a problem occurs.
Indeed, both issues are linked since the more our machines will use automation and motion control, the better operators will be guided. It is a natural development which is still hindered by a war on investment costs (CAPEX) whereas operational costs (OPEX) should also be considered. Performance is a whole.
Smart machines will also ensure much better compliance (machine and process capability) and product traceability, as well as reduce the energy consumption of production lines. All of these needs are fundamental to our industry.”
What are the first steps ?
TD: “To become smarter, our machines above all need more mecatronics in a well thought automation architecture. It is a cultural change for OEMs. Serac is increasing its resources in automation and mecatronics. It is an important part of our 4.0 strategy as all starts with collecting the right data.
We have also decided to bet on decentralized intelligence so as to be able to collect data and control the movement as close as possible to the actuator. This automation architecture offers a maximum of possibilities, flexibility and performance since it allows to process data locally, which is essential for us.
With such an architecture, it is also possible to provide intelligence on installed machinery by upgrading axis functions.”
“ This win-win approach will help us learning more from our machines in use and our algorithms (also called Artificial Intelligence) will be easy to install and update locally, with minimum remote connection. “
Will all production data be stored on cloud servers ?
TD: “No. It would be absurd from an ecological point of view as well as risky, but above all it would be of little use. We will get much better results, and more quickly, using a ‹ small data › approach. That is by selecting the data we need to solve a given problem and processing them on the machine level. This will avoid congesting networks and will reduce response time. Controllers embedded in motion control systems are now real PCs fully capable of analyzing deviations, detecting abnormal behaviour on actuators, and even correcting them (if possible). Artificial (or augmented) intelligence is not new.
Of course, if we want to develop comprehensive algorithms for predictive maintenance, we will have to use IoT, which requires that our customers agree on sharing some data with us. On this point as well, we want to work with them on win-win solutions and collect only useful and shareable data. We are also working on data storage, on how to anonymize, encrypt and process them to offer ultimate security and avoid being hands tied with a SaaS (Software as a Service) solution. We want to secure confidentiality all along the data chain.
This win-win approach will help us learn more from our machines in use and our algorithms (also called Artificial Intelligence) will be easy to install and update locally, with minimum remote connection.”
How is Serac planning to assist customers ?
TD: “By being attentive to their particular needs. Most of international leaders have initiated their own path towards Industry 4.0 and have dedicated teams to implement it. We offer them to integrate our machines in their own architecture, fulfilling their requirements and serving the objectives they’ve defined for their connected factories.
SMEs are rather looking for advice and turnkey solutions. We offer them to tackle some precise improvement points to begin with their digital transformation and gain experience before implementing digital solutions on a wider scale.”
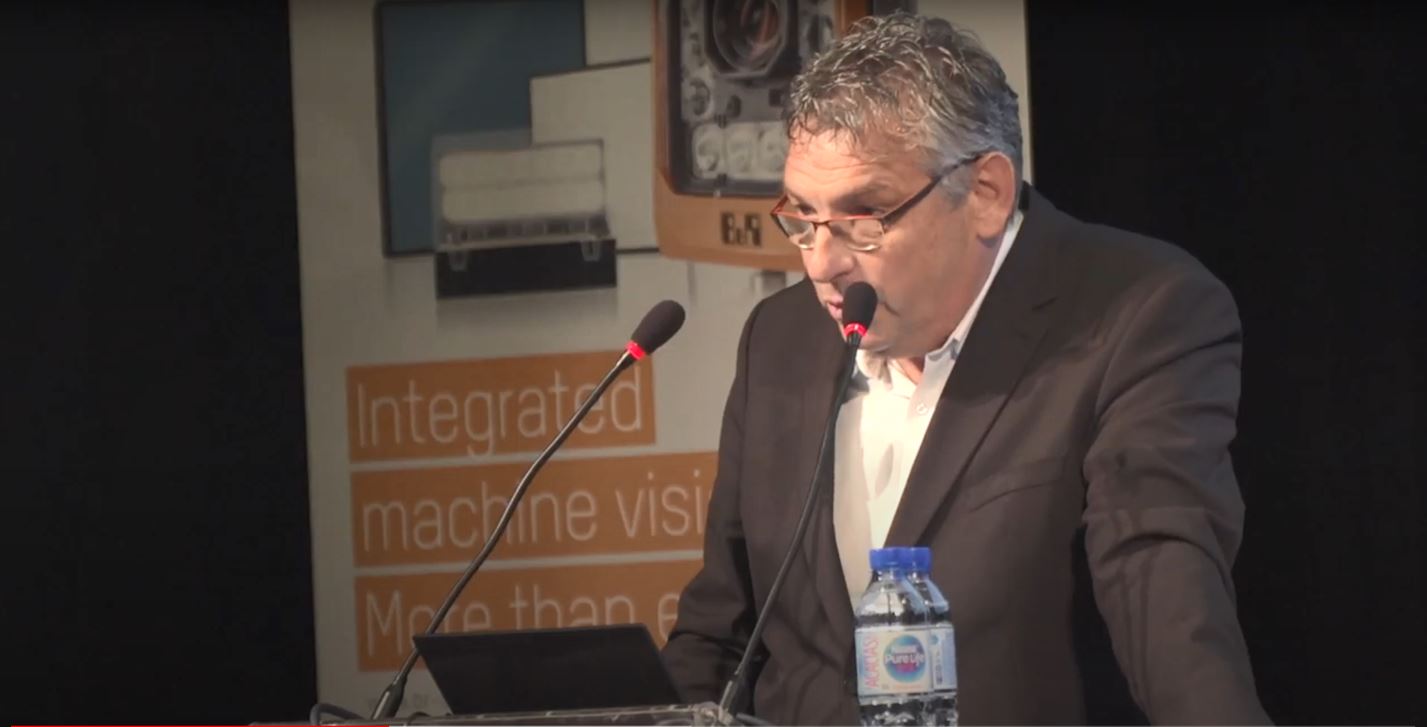
Thierry Deau – Speaker at the “Innovation Days 2019 ” organised by B&R